FORMIGA P 110
Compact-class Additive Manufacturing system that offers a cost-efficient and highly productive entry into the world of Additive Manufacturing.
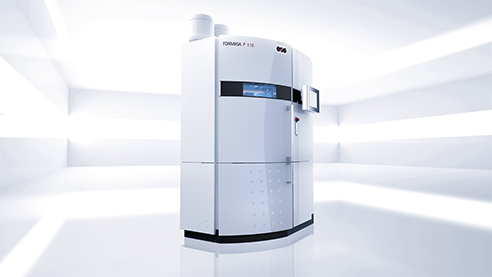
FORMIGA P 110 is a flexible, cost-efficient and highly productive system for the Additive Manufacturing of polymer parts.
This compact system is ideal as an entry into Additive Manufacturing, for example for cost-efficient small series production, customised products with complex geometries and rapid prototyping applications.
Without requiring tools, the system makes direct use of digital CAD data to produce polymer parts of the highest surface quality to a maximum construction height of 330 mm.
Innovation
- Additive Manufacturing of polymer products directly from CAD data within just a few hours
- Cost-efficient, batch-size appropriate production
- Flexible balancing of component requirements (mechanical criteria, surface quality, consistency of form, etc.) with the greatest possible cost efficiency through the use of suitable EOS parameter sets
Quality
- Maximum reproducible part quality that has set quality standards in the market (“FORMIGA Quality”)
- Optimised thermal management (improved dosing tray tempering and new 4-channel heating)
Sustainability
- The material portfolio available for the FORMIGA P 110 particularly encompasses materials with a high level of recyclability, thus reducing costs and protecting the environment
- During system development particular attention has been paid to low operating costs thanks to minimised energy consumption
- An external nitrogen connection enables connection to a central nitrogen supply, reducing the amount of compressed air required by the machine
Efficiency
- Shortened cycle times thanks to the optimisation of the laser sintering process steps
- Minimum downtimes thanks to the streaming concept: The system can start building the job as soon as the job file is loaded
- Optimum usability of the construction space thanks to an improved thermal management system
Flexibility
- Easy integration in existing production environments
- A wide range of materials is available (PA 2200, PA 2201, PA 3200 GF, PrimeCast 101, PA 2105 and various other materials in planning)
- PA 2200 is now also available in 0.06 and 0,12 mm layer thicknesses, as well as 0.1 mm
User-friendliness
- Convenient handling through a high degree of automation and intuitive user interface
- Design for low-dust, ergonomic work conditions
- Data can be prepared in a convenient way in the workplace
Technical Data
FORMIGA P 110 |
|
Effective building volume |
200 mm x 250 mm x 330 mm |
Building speed (depending on material) |
up to 20 mm/h (0.79 in/h) |
Layer thickness (depending on material) |
0.06 mm, 0.1 mm, 0.12 mm (0.0024 in, 0.0039 in, 0.0047 in) |
Support structure |
not required |
Laser type |
CO2, 30 W |
Precision optics |
F-theta lens |
Scan speed during building |
up to 5 m/s (16.4 ft/s) |
Power supply |
16 A |
Power consumption |
2 kW |
Nitrogen generator incl. external nitrogen connection |
integrated |
Compressed air supply |
min. 6 000 hPa (87 psi); 10 m3/h (13.08 m3) |
Dimensions (W x D x H) |
|
System incl. powder containers and touch screen |
1 320 mm x 1 067 mm x 2 204 mm (51.97 in x 42.01 in x 86.77 in) |
Recommended installation space |
3.20 m x 3.50 m x 3.0 m (126 in x 137.8 in x 118.1 in) |
Weight |
approx. 600 kg (1.323 lb.) |
Unpacking and sieving station (optional) |
1 200 mm x 700 mm x 1 500 mm (47.24 in x 27.56 in x 59.06 in) |
Powder mixing station (optional) |
700 mm x 500 mm x 1,000 mm (27.56 in x 19.69 in x 39.37 in) |
Data preparation |
|
Software |
EOS RP Tools (optional); Desktop PSW |
CAD interface |
STL (optional: converter to all common formats) |
Network |
Ethernet |